QUALITY AS THE CORE OF OUR OPERATIONS
Quality is not just an objective for us, but an ongoing process that permeates every aspect of our business. Our dedication to quality is evident at every stage of our production cycle, from the initial design and procurement of raw materials to the final shipping of products. By upholding rigorous quality standards and providing continuous training, we ensure that our products not only meet legal regulations but also exceed customer expectations. Additionally, we conduct regular audits and quality checks to maintain the highest safety standards. Through our supplier management program, we ensure our partners receive continual training, keeping them informed about current EU regulations and maintaining consistent production quality.DIGITAL TECHNOLOGIES FOR CONTINUOUS PROCESS IMPROVEMENT
By using state-of-the-art technology, we are constantly improving the efficiency and quality of our processes. Our advanced quality assurance system allows us to optimize the supply chain through user-friendly tools. With this toolkit, we standardize our processes, allowing inspections to be carried out faster and more accurately. Before shipping a product, each container is thoroughly inspected by our quality control team. If there are discrepancies, product management can react quickly by directly contacting the on-site quality control. In this way, possible complaints can be resolved in advance and unnecessary time and expense is avoided.Through targeted risk assessments, regular customer satisfaction measurements and continuous optimization of our processes, we ensure that our products and services always meet the highest standards. Our quality assurance tool allows us to provide more accurate documentation, greater transparency and better traceability of all processes. These efficiency gains allow us to respond quickly to our customers' needs while continuously improving product quality. This allows us to optimize our internal processes and continuously achieve the highest quality of our products.
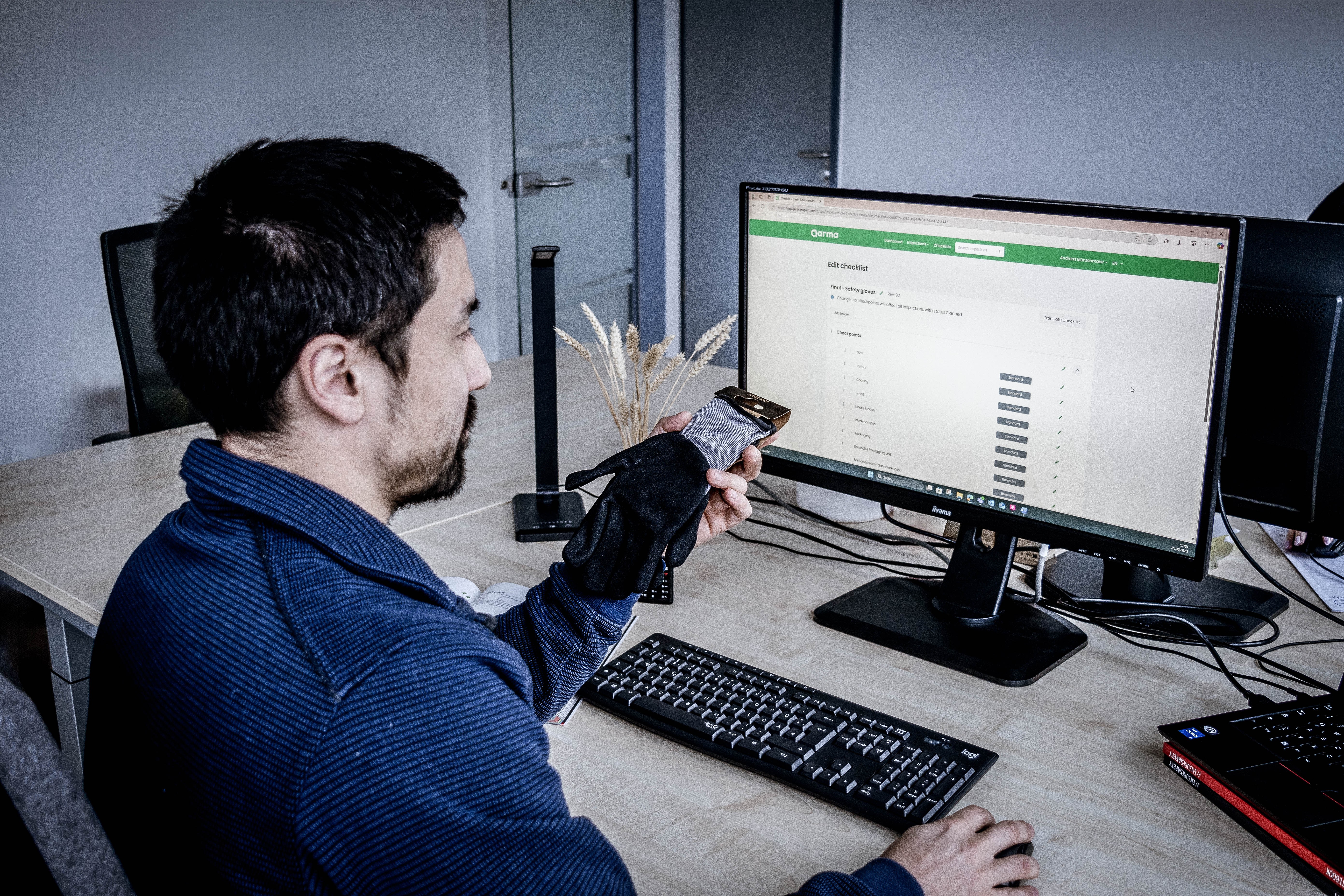
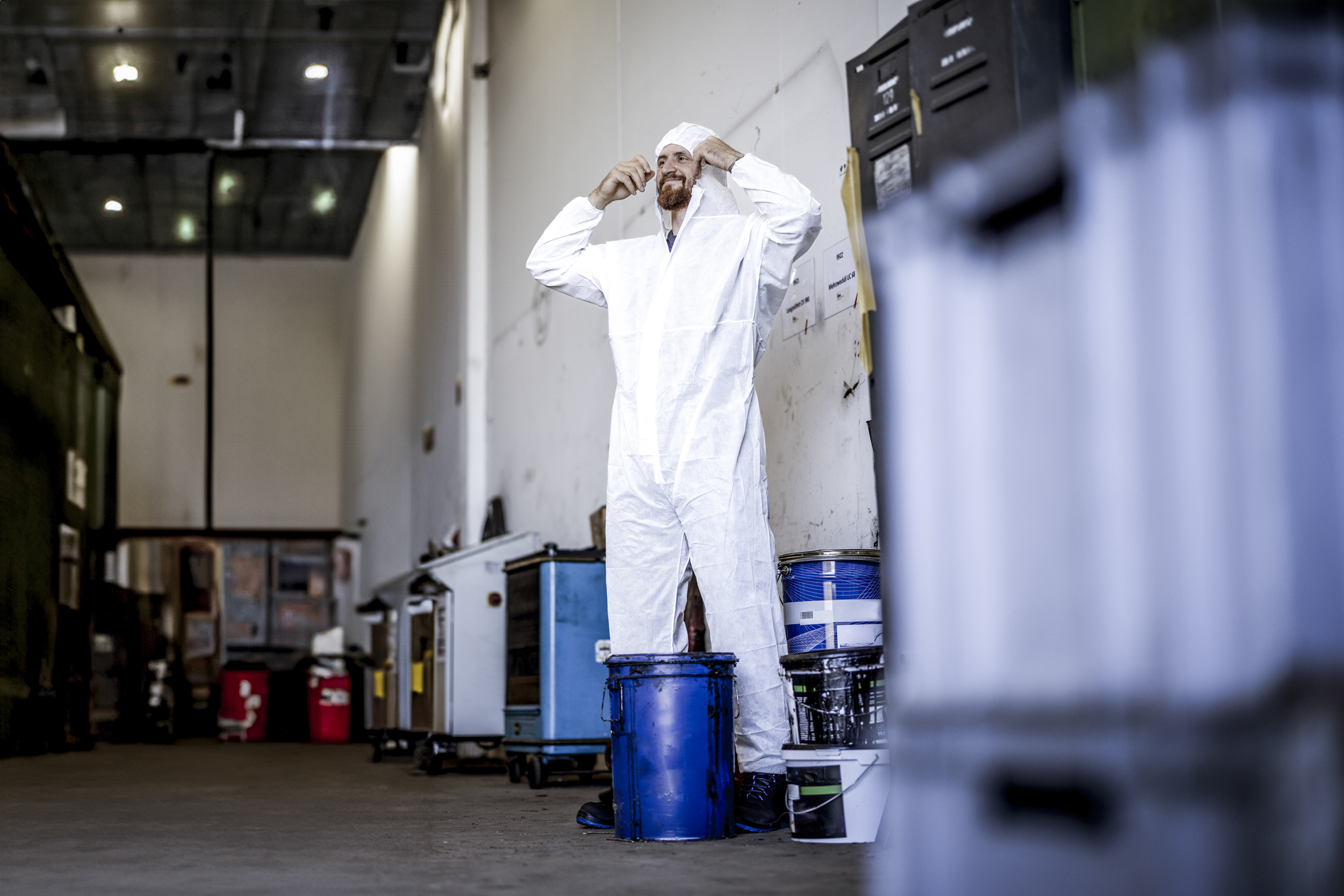
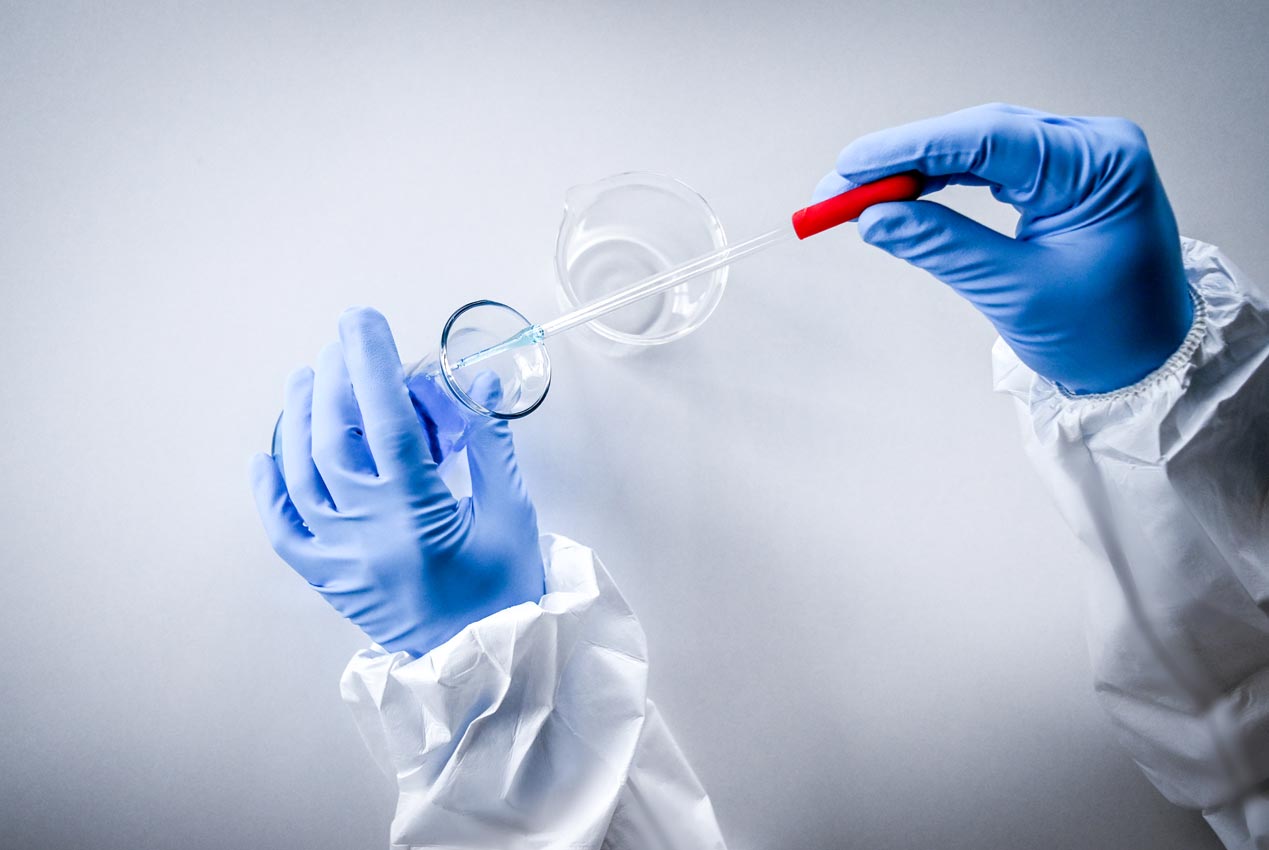
ADVANCED QUALITY ASSURANCE THROUGH LABORATORY TESTING
To meet the high standards of our quality management system, we conduct product testing in the laboratory located in our new building. Systematic testing and analysis allow us to adhere to quality standards and detect deviations early in the process. Key activities in our laboratory include:1. Sampling tests
2. Tests and measurements to assess physical, chemical, and microbiological properties
3. Calibration and validation: Regular inspections and adjustments of testing equipment and methodologies
4. Quality audits: Routine internal and external audits of the laboratory
5. Training and development: Ongoing education for laboratory staff
These actions ensure not only the quality of our products but also the high efficiency and precision of our entire production process. Our well-managed laboratory plays a crucial role within our quality management system, helping to identify and resolve potential issues at an early stage.
NAVIGATING NEW CHALLENGES AND OPPORTUNITIES
Innovative advancements in quality management are bringing both new challenges and opportunities to us and many other companies. These developments provide fresh perspectives for organizations looking to tackle future challenges head-on. Not only do they enhance the efficiency of quality management, but they also lay the foundation for a sustainable, forward-thinking business model. We aim to identify and seize these opportunities to thrive in a competitive market while also contributing positively to society.The extended producer responsibility (EPR) requires us to take responsibility for the collection, recycling, and proper disposal of packaging waste, thereby supporting sustainability within the industry.
The ISO 9001 update in December 2025 aims to address current challenges and emerging trends. The following innovations are expected to drive progress in quality management going forward:
1. Emphasis on guidance
2. Integration of global changes and emerging technologies
3. In-depth review of quality management principles
4. Extensive involvement of experts
The rise of digital tools and automation is transforming how we optimize processes and eliminate errors. Artificial intelligence is key in this shift, offering precise analysis of quality data and enabling businesses to make data-driven, strategic decisions.
YOUR PARTNER FOR BEST QUALITY
Through our quality management system, we are committed to ensuring the highest quality of our products while consistently meeting customer expectations. Our robust QM framework also ensures that all our products and services adhere to the necessary standards. By doing so, we position ourselves to successfully navigate both current and future challenges driven by globalization and digitalization.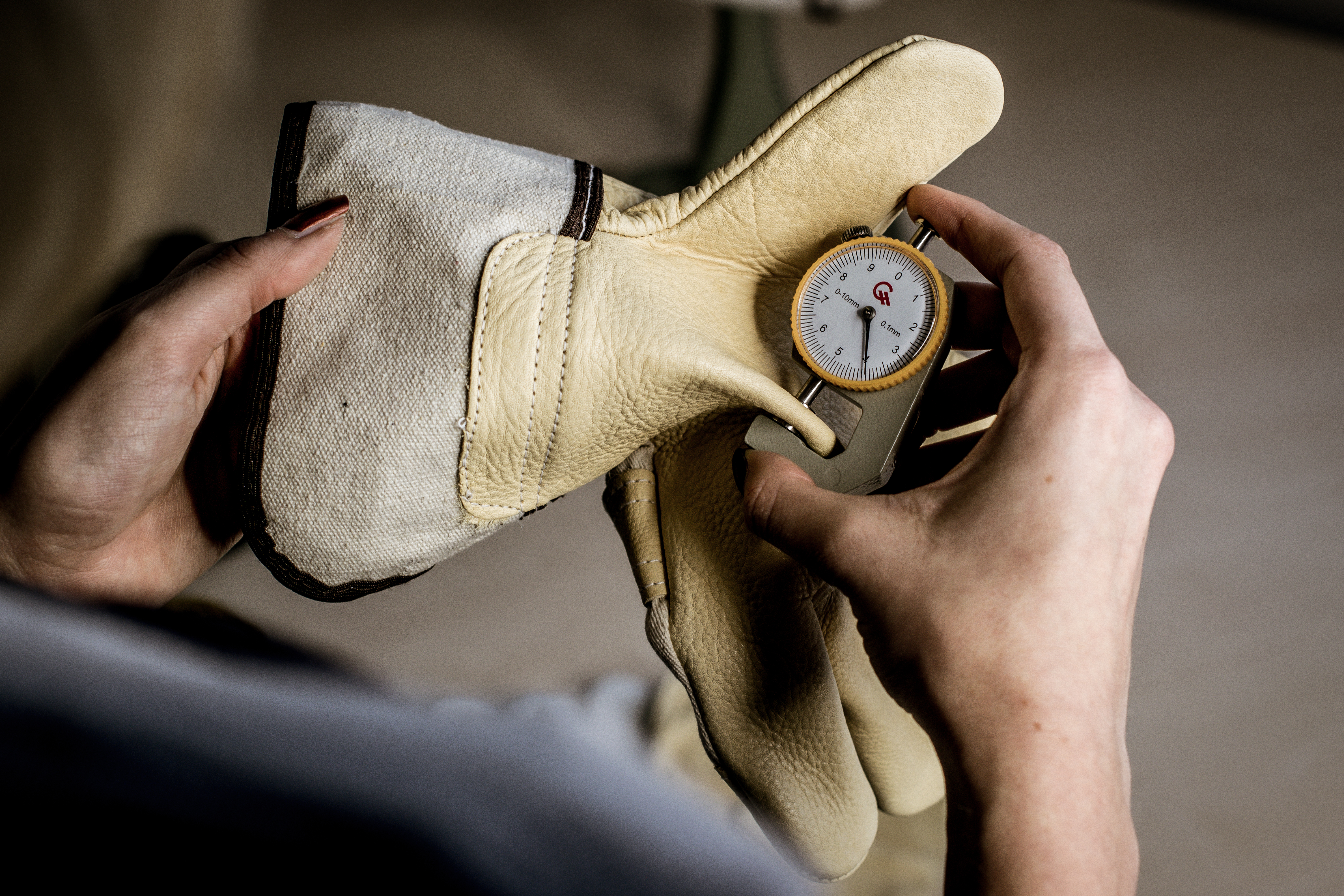
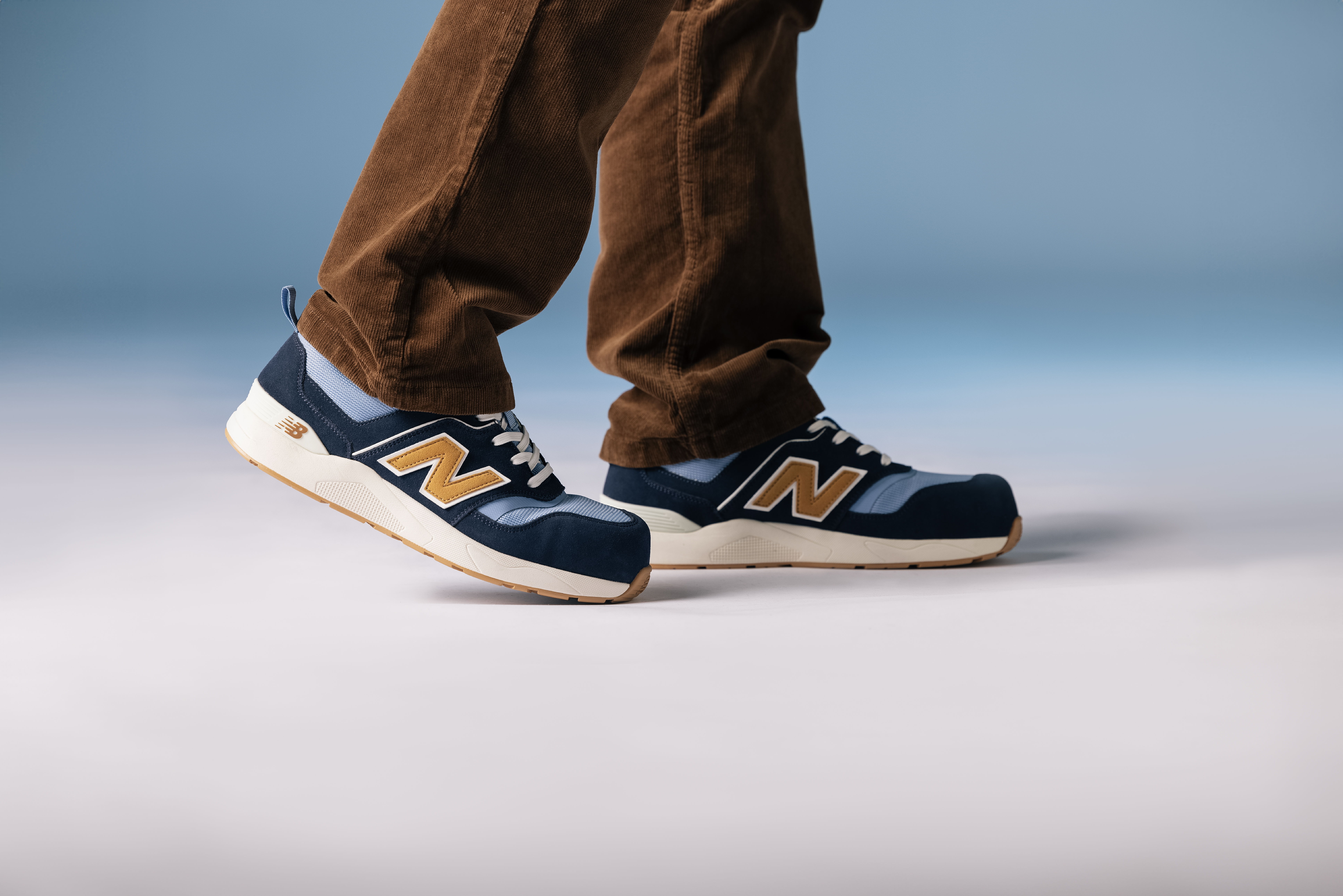